Custom-made protective uniforms are always the optimal solution to elevate your company’s image. In a working environment that increasingly demands higher safety standards, equipping employees with tailor-made protective clothing is not only a way to safeguard workers, but also an effective branding strategy. Uniforms are more than just garments – they represent professionalism, responsibility, and corporate unity.
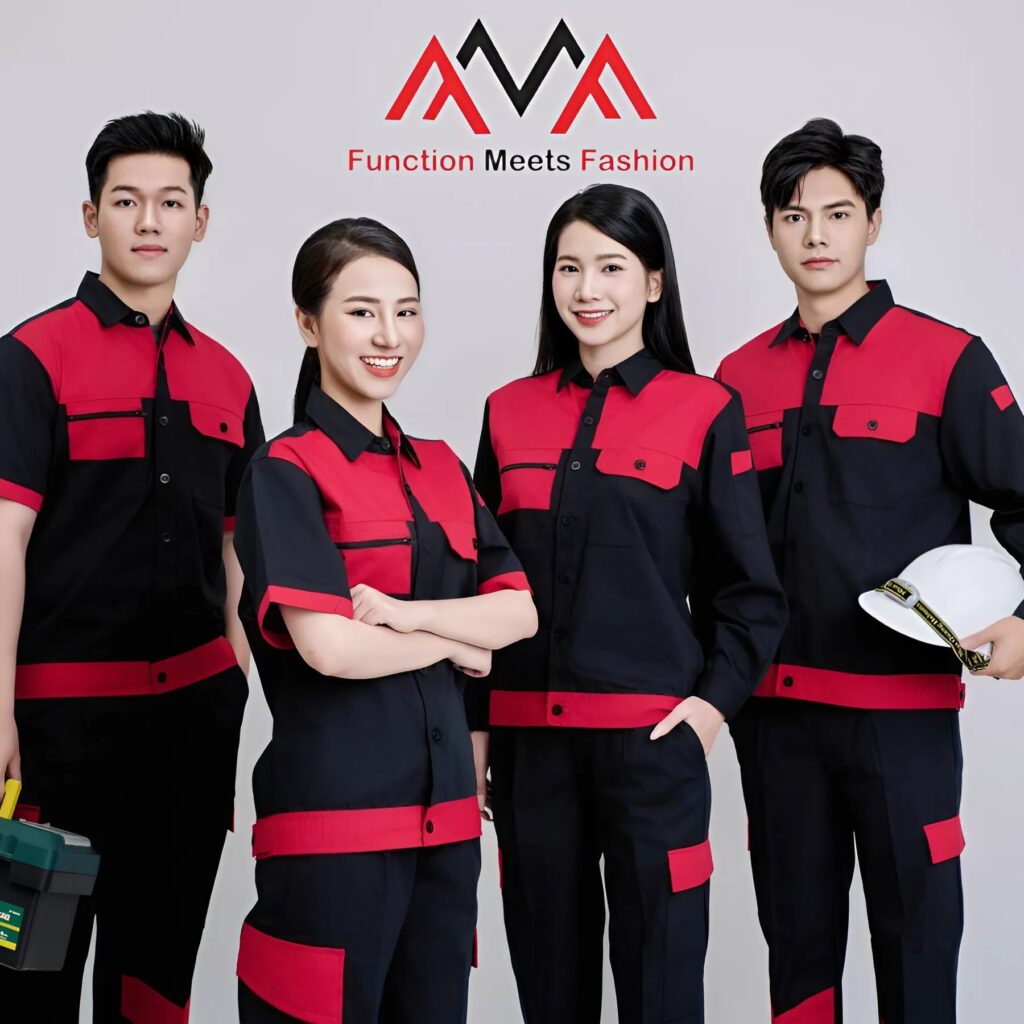
You might also be interested in: FMF Standard-Compliant Safety Workwear
1. What Are Custom-Made Protective Uniforms?
Custom-made protective uniforms are safety garments specifically designed and manufactured based on the individual requirements of each business, industry, or job role. Unlike mass-produced uniforms, these uniforms are highly personalized to suit working environments, meet safety standards, and reinforce corporate identity.
Common elements of customization include:
-
Fabric material: fire-resistant, anti-static, sweat-absorbent, impact-resistant, etc.
-
Design and color: aligned with company culture and job characteristics.
-
Branding/logo: printed or embroidered directly on shirts, pants, caps, etc.
-
Additional features: reflective strips, utility pockets, specialty collars, etc.
2. The Role of Custom-Made Protective Uniforms in Businesses
2.1 Ensuring Workplace Safety
This is the core function of protective uniforms. Each industry has unique risks, and custom designs help:
-
Protect workers from high temperatures, chemicals, dust, and more.
-
Enhance functionality: utility pockets, sturdy zippers, durable stitching.
-
Improve visibility in low-light environments through reflective elements.
2.2 Enhancing Professionalism and Brand Image
Uniforms act as the “face” of your business. When well-designed with sharp logos and consistent colors, they help:
-
Make a positive impression on partners and customers.
-
Reinforce your brand value to the public.
-
Boost employee morale and promote workplace discipline.
2.3 Long-Term Cost Optimization
Investing in high-quality, custom-made protective uniforms tailored to your actual needs allows businesses to:
-
Reduce maintenance and replacement costs.
-
Control quality and quantity proactively.
-
Easily reorder with consistency when expanding the workforce.
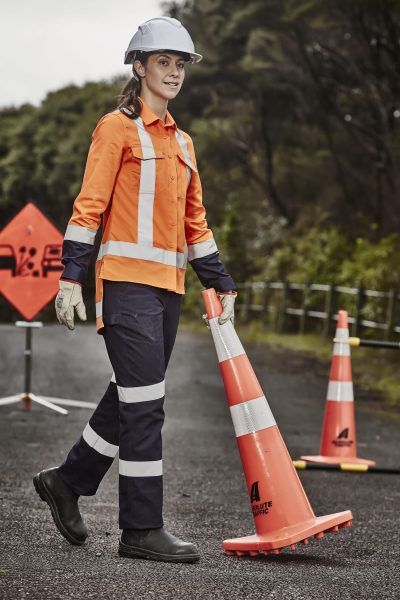
3. Industries That Need Custom-Made Protective Uniforms
✔ Construction & Engineering
-
Thick, tear-resistant, impact-proof fabric.
-
Reflective jackets and matching protective headwear.
-
Large pockets and strong zippers for tool storage.
✔ Mechanical & Welding Industries
-
Flame-resistant and spark-proof materials.
-
Sturdy, well-sealed stitching to shield the skin from sparks.
✔ Electricity & Telecommunications
-
Lightweight, breathable anti-static fabrics.
-
Integration with gloves, helmets, and other gear.
✔ Food Processing, Healthcare, Clean Rooms
-
Antibacterial fabrics that are easy to clean.
-
Light, clean colors (white, light blue, etc.)
-
Simple designs for convenience in movement.
✔ Warehousing, Transport, and Logistics
-
Durable, lightweight, and flexible fabric.
-
Easy-to-recognize color schemes and designs.
-
Equipped with reflective elements and dust resistance.
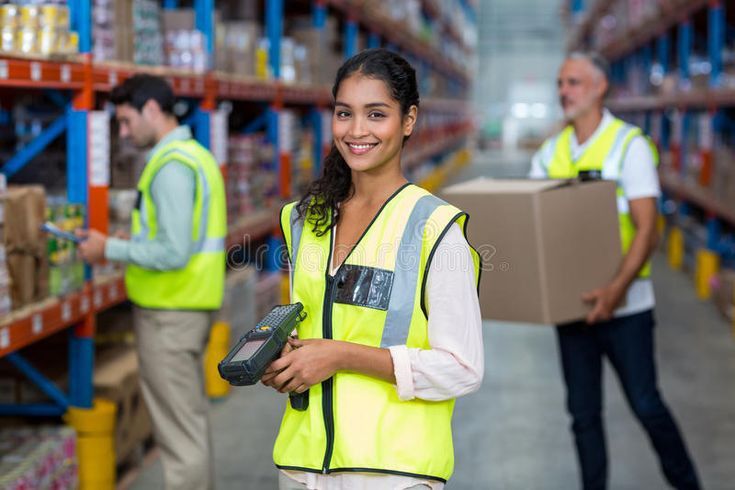
4. Custom Protective Uniform Design & Production Process
A standardized process helps businesses manage both quality and progress. The steps include:
Step 1: Information Gathering & Consultation
-
Understand industry type, workforce size, and working conditions.
-
Suggest suitable materials, designs, and budgets.
Step 2: Design & Sample Approval
-
Provide 2D design mockups, color schemes, logo placement, etc.
-
Submit physical samples or design files for approval before mass production.
Step 3: Production
-
Manufacture according to the approved design.
-
Inspect every stage for consistency and quality.
Step 4: Delivery & After-Sales Support
-
Timely and direct delivery.
-
Returns or exchanges supported for defective items.
-
Store designs for future reorders.
5. Criteria for Choosing a Custom Protective Uniform Supplier
When selecting a supplier, companies should consider the following:
5.1 Experience and Reputation
-
Years of experience in uniform manufacturing.
-
Own production facilities and professional design teams.
5.2 Product Quality
-
Wide range of fabrics: kaki, cotton, fire-resistant, etc.
-
Durable stitching, accurate sizing, sharp printing or embroidery.
5.3 Customer Service
-
Dedicated consultation and design support.
-
Transparent pricing and delivery timelines.
-
Clear warranty and return policies.
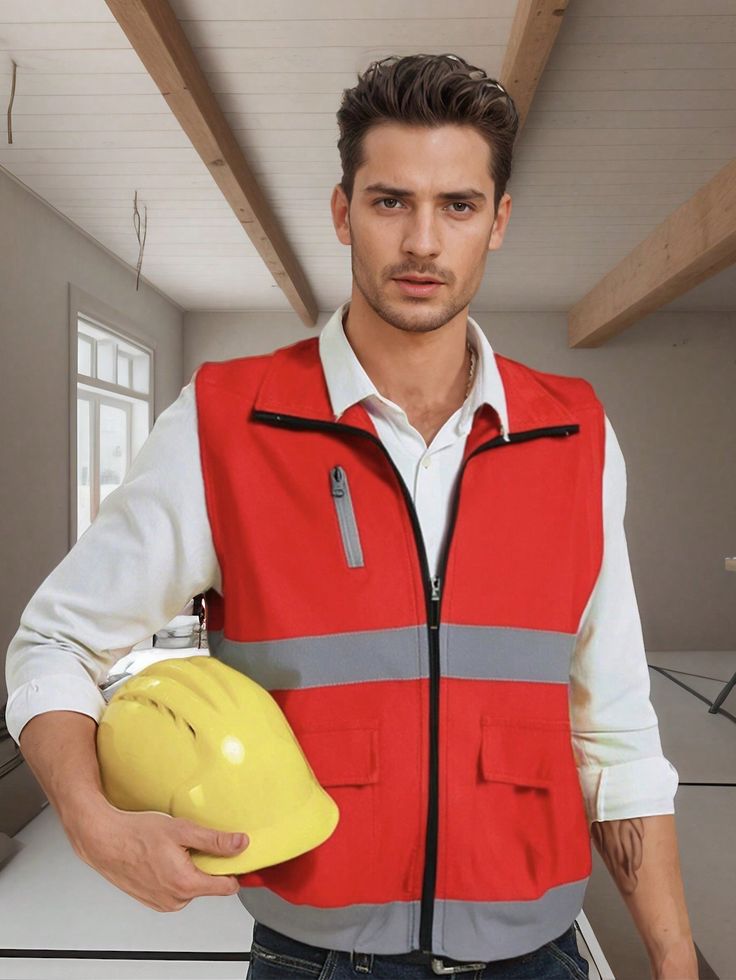
5.4 Reasonable Pricing
-
Competitive pricing suitable for business scale.
-
Discounts available for large orders.
6. Conclusion
Custom-made protective uniforms are more than just safety gear — they are a vital asset in portraying professionalism, corporate culture, and brand value. Investing in well-designed, personalized uniforms is a strategic long-term solution that not only enhances workplace safety but also optimizes costs and solidifies your company’s unique identity.
If you’re looking for a solution that combines flexibility, aesthetics, and safety, custom-made protective uniforms are the ideal choice. It’s a strategic move that reflects serious investment in your people, your image, and your future.
You might also be interested in: Reflective Safety Uniforms for Construction Engineers
Sản phẩm
Red And Black Short-Sleeve Workwear Set
Red And Black Long-Sleeve Workwear Set
Blue And Grey Short-sleeve workwear set
BLUE+GREY LONG-SLEEVED WORKSUIT
CHARCOAL+GREY SHORT-SLEEVED WORKWEAR
CHARCOAL+GREY LONG-SLEEVED WORKWEAR
SHORT-SLEEVED REFLECTIVE GRAY WORKSUIT
LONG-SLEEVED REFLECTIVE GRAY WORKSUIT
GREY COORDINATE LONG-SLEEVED NAVY
NAVY POLO JERSEY
POLO BLUE+NAVY JERSEYS FOR MEN AND WOMEN
POLO JERSEY NAVY+WHITE MEN’S/WOMEN’S